Ogee Profiles
Prior to the advent of large cast iron machinery produced by a handful of companies in the United States, sash windows varied greatly depending on the region you were living in and who the local joiners and carpenters were. The ogee profile, which is the classic s-shaped profile found on architectural millwork, was not standardized, and much of the profiling that was done was preformed with a moulding plane.
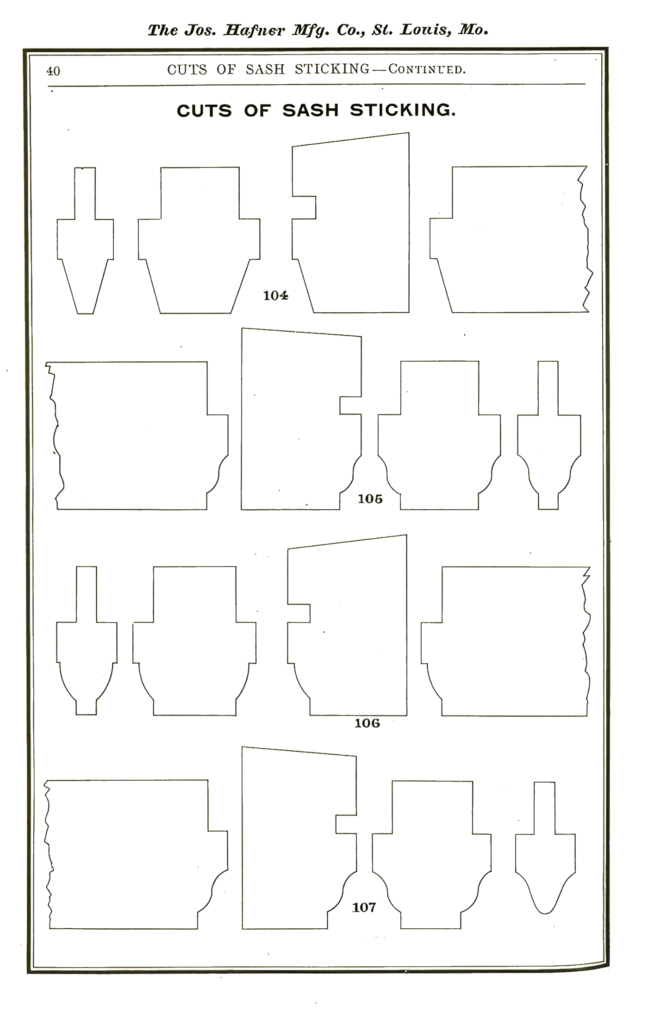
The Ogee No 5 profile became the standard for most homes built between 1875-1960 and is still used today on router and shaper bits that we use to reproduce these windows.
Segway On How Ogee Profiles are Intended to Be Used
Ogee profiles are typically categorized as either Cyma Recta (Latin: upright wave) or Cyma Reversa (Latin: reversed wave).
To understand how these profiles are intended to be used, we need to introduce a few more terms.
The Cavetto is the hollow portion of the curve and is a terminating molding.
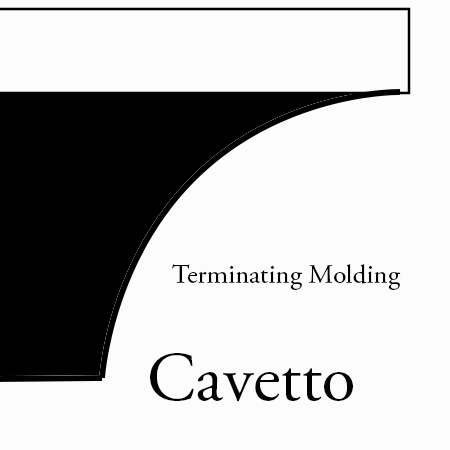
The Ovolo is a convex curve and is a supporting molding.
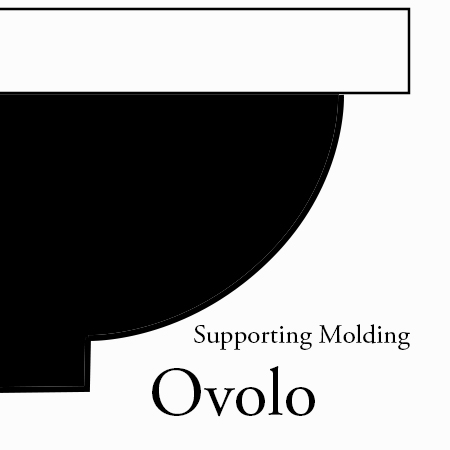
The Cyma Reversa and Cyma Recta incorporate the two curves and depending on wheather the last curve is a hollow or a convex curve dictates its intended use.
Cyma Reversa (Latin: reversed wave) Notice the Ovalo curve at the end.
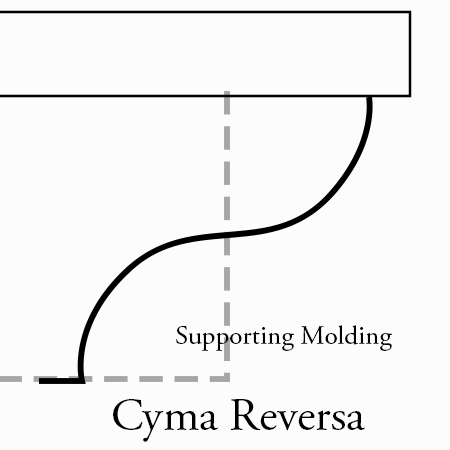
Cyma Recta (Latin: upright wave) Notice the Cavetto curve at the top of this profile, which makes its inteded use as a terminating molding. Commonly found in a crown molding or a terminating molding on the top of a wardrobe.
If you want to explore this subject further this video does a great job explaining the topic.
The Evolution of Sash Sticker Machines: From Handcraft to Industrial Precision
The development of sash sticker machines played a crucial role in the industrialization of woodworking, particularly in the production of sash windows. These machines transformed the process from a labor-intensive craft to an efficient, repeatable system capable of producing high-quality window components on a large scale. Among the most notable early machines were the American Sash Sticker No. 3 1/2 and No. 2 1/2, which laid the groundwork for larger, more advanced models like the Oliver 4 1/2 Machine. This article explores the history, functionality, and impact of these machines on woodworking and architectural millwork.
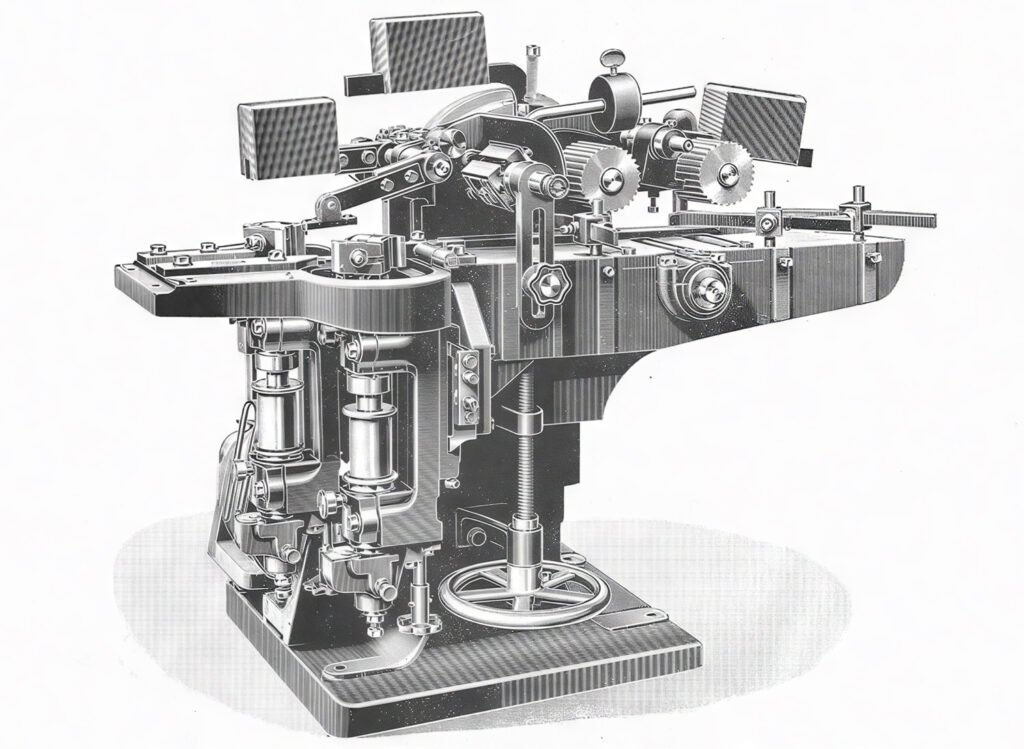
The Origins of Sash Milling Machines
Before the invention of dedicated sash-making machines, craftsmen relied on molding planes to create intricate sash profiles. Each piece had to be shaped by hand, requiring significant time and skill. As demand for windows increased with urban expansion and industrialization, the need for mechanized production became evident.
Despite this change in the production equipment that was used, molding planes continue to be a popular tool for hand tool work enthusiasts and are available to purchase from several reputable sellers. M.S. Bickford, Heartwood Tools, and Garrett Wade.
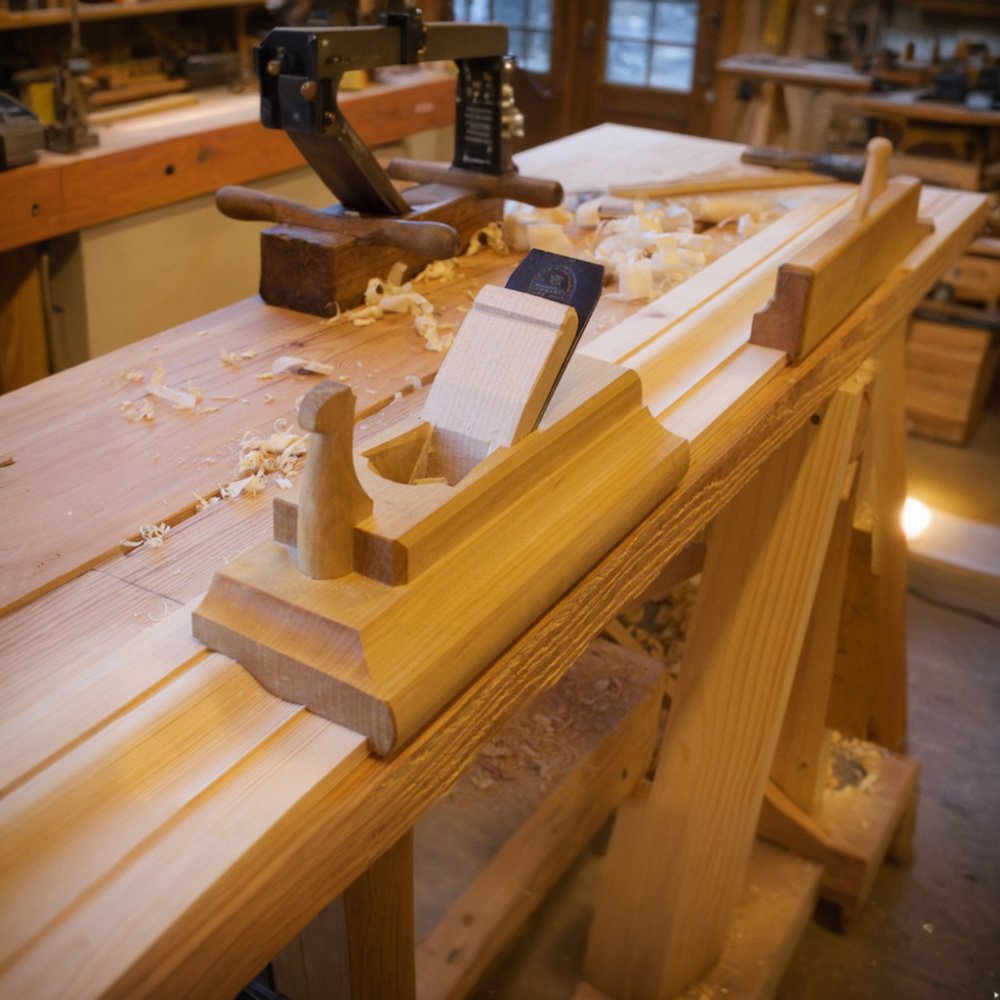
By the mid-19th century, steam-powered and belt-driven machinery began revolutionizing woodworking. Sash sticker machines emerged as specialized tools that could precisely cut, shape, and mill window components with remarkable efficiency. Among the earliest adopters were American manufacturers producing machines tailored to the growing millwork industry.
American Sash Sticker No. 3 1/2: The Workhorse of Mid-Sized Shops
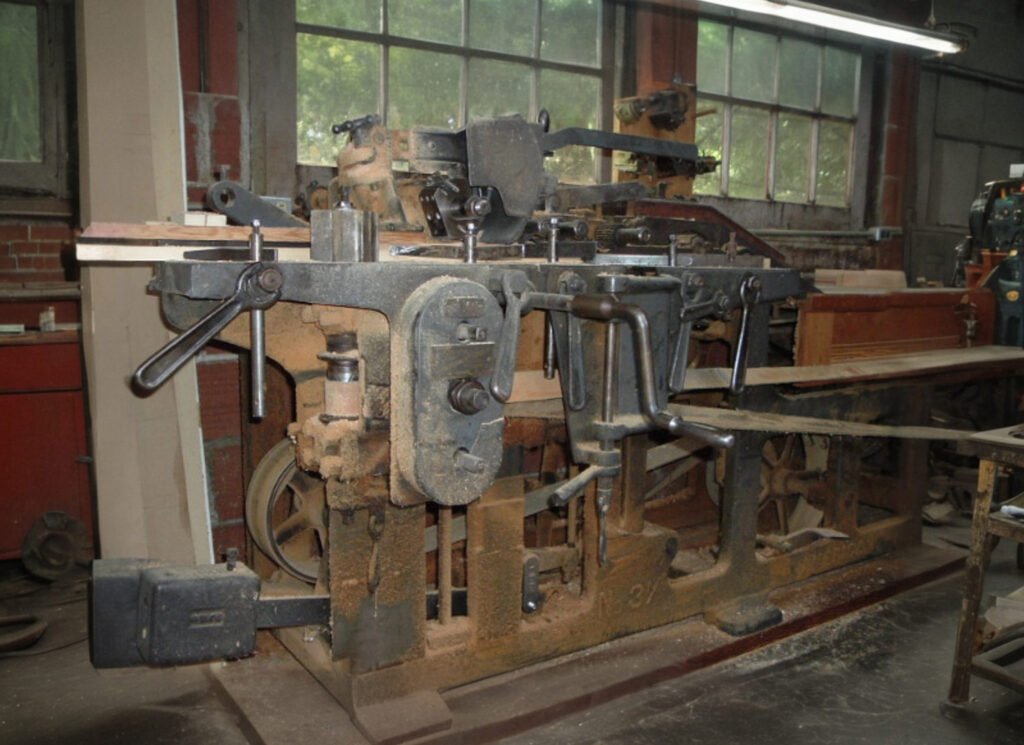
The No. 3 1/2 Sash Sticker was designed for small to mid-sized woodworking operations, balancing precision and productivity. This machine was belt-driven and excelled at shaping sash bars, muntins, and window components.
Features:
- Sturdy Cast Iron Frame – Ensured stability and minimized vibrations for clean cuts.
- Multiple Cutterheads – Allowed intricate shaping of sash profiles and decorative elements in one pass.
- Adjustable Fence & Guides – Enabled flexibility for different sash dimensions and profiles.
- Handwheel Adjustments – Provided fine-tuning for accurate depth and profile shaping.
- Counter-Weighted Mechanism – Allowed for smoother operation and reduced cutterhead stress.
Impact on Window Manufacturing:
The No. 3 1/2 was a staple in sash window production, particularly for double-hung and multi-pane sash windows. Its ability to handle both softwood and hardwood made it a preferred choice for manufacturers producing windows in a variety of architectural styles.
American Sash Sticker No. 2 1/2: Precision for Small Shops
For smaller woodworking operations and independent craftsmen, the No. 2 1/2 Sash Sticker provided a compact, reliable alternative.
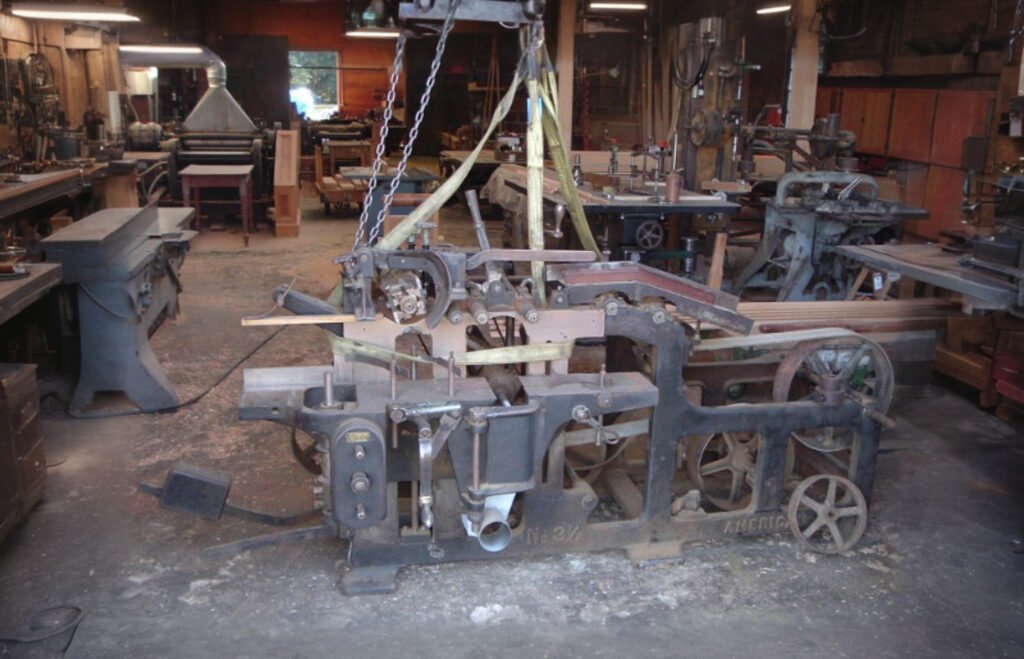
Features:
- Compact Design – Ideal for workshops with limited space.
- Single Cutterhead Operation – Required multiple passes for complex profiles but allowed customization.
- Hand-Operated Feed Mechanism – Gave operators full control over intricate detailing.
- Simple Belt-Driven System – Made maintenance and repair straightforward.
Use in Traditional Woodworking:
The No. 2 1/2 was particularly favored by craftsmen restoring historic buildings, as it could precisely replicate traditional sash profiles. Its ability to produce custom windows for homes, churches, and specialty projects ensured its enduring legacy.
The Oliver 4 1/2 Sash Sticker: The Next Step in Industrial Evolution
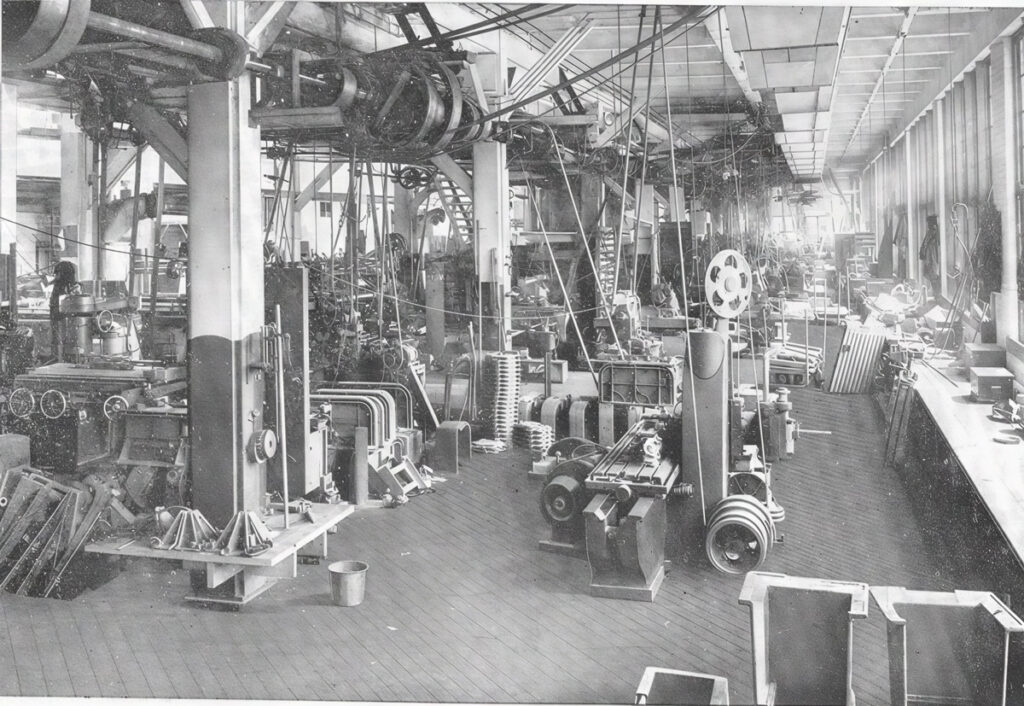
As demand for mass-produced sash windows increased, manufacturers needed machines capable of higher output with even greater accuracy. The Oliver 4 1/2 Sash Sticker represented the next step in this evolution.
Key Advancements:
- Larger Capacity – The 4 1/2-inch reference indicated its ability to handle wider sash bars and rails, making it ideal for factory-scale production.
- Multiple Cutter Heads – Reduced the number of passes needed to shape complex profiles.
- Enhanced Power System – As electric motors replaced steam power, the Oliver 4 1/2 became more efficient and easier to operate.
- Cast Iron Stability – Like its predecessors, the Oliver machine was built for durability and precision, ensuring minimal vibration and maximum consistency.
Impact on the Window Industry:
The Oliver 4 1/2 machine was widely adopted in sash window factories, streamlining production and helping to standardize window manufacturing. Its ability to produce high volumes without sacrificing quality made it an industry favorite, particularly in the early 20th century when large-scale residential and commercial construction boomed.
Comparison of Key Sash Sticker Machines
Feature | No. 3 1/2 Sash Sticker | No. 2 1/2 Sash Sticker | Oliver 4 1/2 Sash Sticker |
---|---|---|---|
Size | Medium-duty | Small-duty | Large-scale production |
Cutterheads | Multiple for complex shaping | Single for precision work | Multiple for efficiency |
Ideal for | Mid-sized factories | Small workshops, restorations | High-volume factory production |
Drive System | Belt-driven | Belt-driven | Electric motor-driven |
Usage | Double-hung sash windows | Custom profiles, historic work | Mass production of sash components |
Precision | High for repeatable work | Manual for detailed custom work | Industrial-grade accuracy |
Legacy and Modern Use
Though modern CNC routers and molding machines have largely replaced early sash sticker machines, their legacy remains strong. Many traditional joinery shops and historic restoration specialists still use and restore vintage sash sticker machines for their unmatched ability to replicate period-correct window profiles.
For those interested in preserving these historic machines, restoration efforts typically involve:
- Reconditioning belt-drive systems for smooth operation.
- Sharpening or replacing cutterheads to match traditional profiles.
- Cleaning and repainting cast iron components to ensure longevity.
- Retrofitting with electric motors for easier modern operation.
Conclusion
The evolution of sash sticker machines—from the American No. 2 1/2 and No. 3 1/2 to the Oliver 4 1/2—reflects the broader transformation of woodworking from artisanal craftsmanship to industrial efficiency. These machines played a vital role in shaping the built environment, providing the precision and speed necessary for large-scale window production while maintaining the fine detail that defines classic architectural styles. Today, they remain valuable tools for those dedicated to preserving historic woodworking techniques and craftsmanship.