The evolution of millwork in the United States is a testament to the nation's ingenuity and adaptability, reflecting broader societal shifts and technological advancements. From handcrafted beginnings to industrialized production, millwork has played a pivotal role in shaping American architecture and interior design.
Early Beginnings: Handcrafted Artistry
In the early days of American settlement, millwork was a labor-intensive craft. Skilled artisans employed hand tools to create functional and decorative wooden elements for buildings. Hand planes allowed craftsmen to smooth and shape wood with precision. These tools, whose origins trace back nearly 2,000 years, were indispensable in producing items like moldings, window frames, and cabinetry. Woodworkers took great pride in their craftsmanship, with early American homes featuring detailed paneling, wainscoting, and intricate joinery, all made by hand in small workshops.
Throughout the 17th and 18th centuries, the demand for millwork grew, particularly as cities expanded and the construction of larger homes and public buildings became more common. Carpenters and joiners formed guilds to regulate the trade, ensuring that only skilled artisans could produce high-quality millwork. Colonial homes often showcased European influences, with Georgian and Federal styles incorporating classical columns, cornices, and decorative trim that required meticulous hand-finishing.
Industrial Revolution: Mechanization and Standardization
The onset of the Industrial Revolution in the late 18th and early 19th centuries marked a significant turning point for millwork. In San Luis Obispo County, California, where I live, you can immediately tell apart the houses that were built in this "Golden Era of Millwork." They make up the majority of the Historic District in downtown and the double-hung sash windows instantly separate them from the new construction.
The introduction of steam-powered machinery revolutionized wood milling processes, increasing production efficiency and consistency. Before this period, millwork had been a bespoke industry, where each piece was hand-crafted to fit individual buildings. With mechanization, however, the ability to mass-produce moldings, doors, windows, and paneling changed the landscape of American construction.
One of the earliest companies to embrace mechanized millwork production was The Curtis Companies, which started in the mid-19th century and became one of the largest manufacturers of architectural millwork in the United States. By utilizing steam-powered saws, planers, and lathes, they were able to supply a growing nation with affordable yet intricate woodwork.
The Victorian Era: The Golden Age of Millwork
Between 1840 and 1910, often referred to as the "Golden Era of Millwork," the industry flourished. Advancements in manufacturing processes, combined with a booming population, spurred demand for residential and commercial buildings adorned with intricate woodwork. The Victorian era, named after Queen Victoria, brought an explosion of highly decorative architectural styles that relied heavily on ornate millwork.
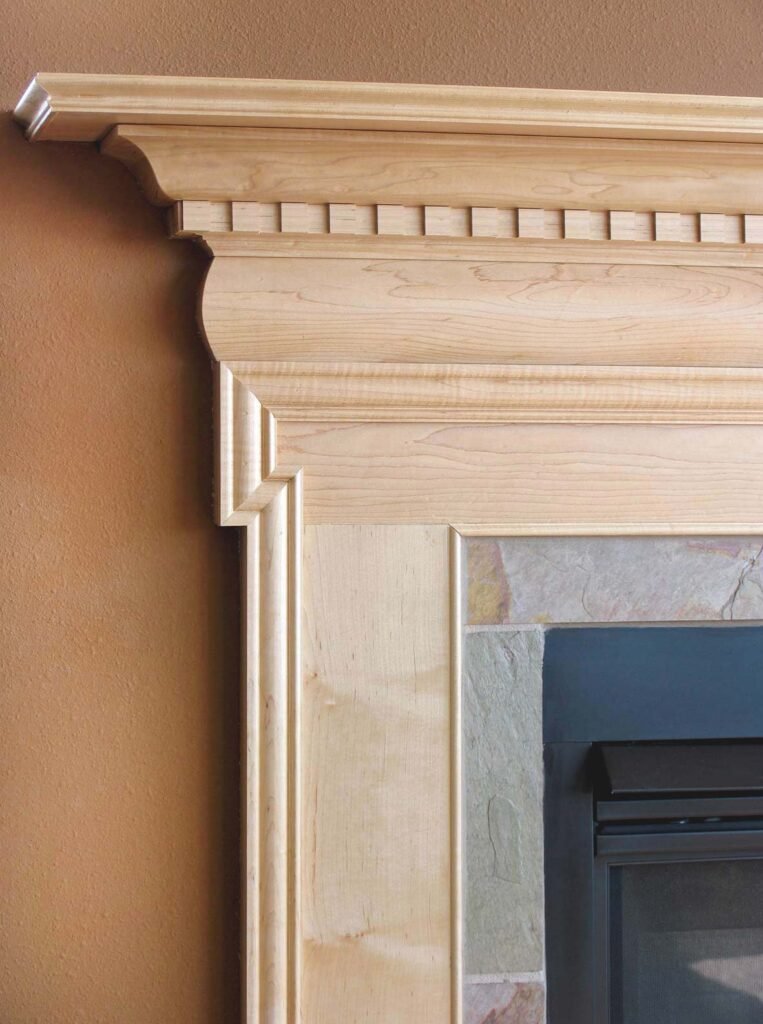
Elements like the pulvinated frieze are not commonly seen in modern millwork but are still used in Historical restoration projects.
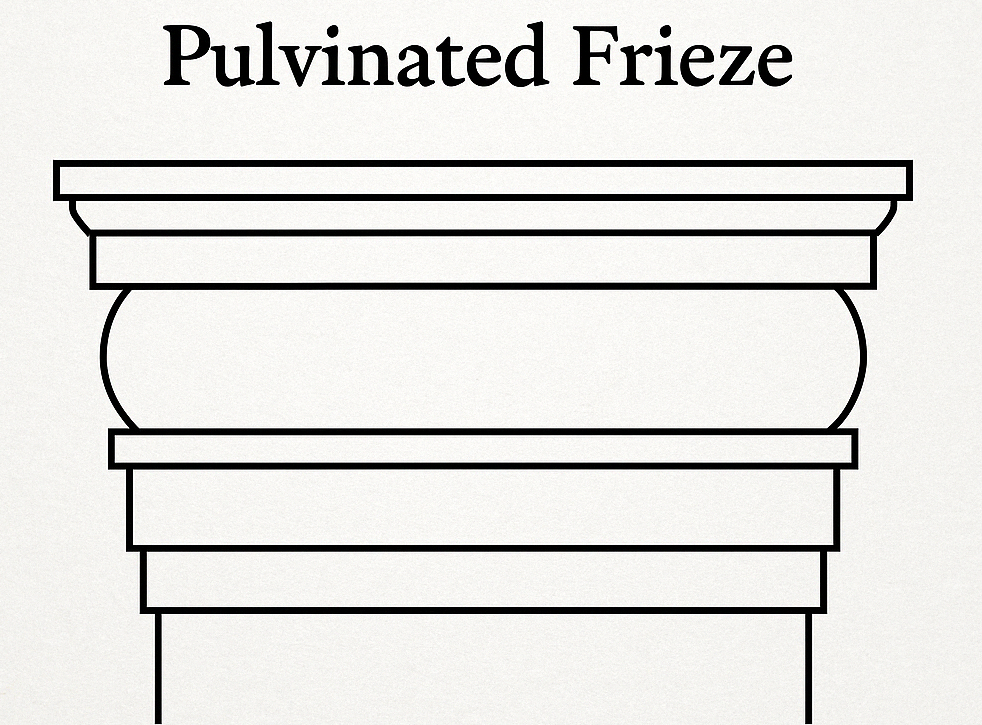
Victorian homes were renowned for their complex detailing, including gingerbread trim, elaborate staircases, wainscoting, and built-in furniture. The use of scroll saws and spindle cutters allowed millwork factories to mass-produce intricate patterns that would have been painstakingly slow to create by hand. Some of the most recognizable styles of the Victorian period included Gothic Revival, Italianate, Queen Anne, and Second Empire, each with its own distinct millwork features.
Notable Architects
Notable architects of the period, such as Henry Hobson Richardson and Richard Morris Hunt, were instrumental in incorporating detailed millwork into their designs. Hunt, who designed grand mansions for America’s elite, worked closely with millwork companies to ensure that interiors featured stunning wood carvings, grand staircases, and highly detailed moldings. Richardson, known for Richardsonian Romanesque architecture, favored bold woodwork, including massive arches and intricately paneled walls.
Major millwork companies thrived during this period, with names like The E.L. Bruce Company and Foster-Munger Company supplying the construction industry with high-quality decorative woodwork. The Morgan Millwork Company, founded in 1892, was another leader in producing exquisite moldings, window casings, and elaborate newel posts, which became the hallmark of upper-class Victorian homes.
One of the most famous examples of Victorian millwork in the United States is the Carson Mansion in Eureka, California. Built in the 1880s for lumber baron William Carson, the home is a masterpiece of Queen Anne-style architecture, featuring extensive millwork in the form of turrets, gables, and decorative spindles.
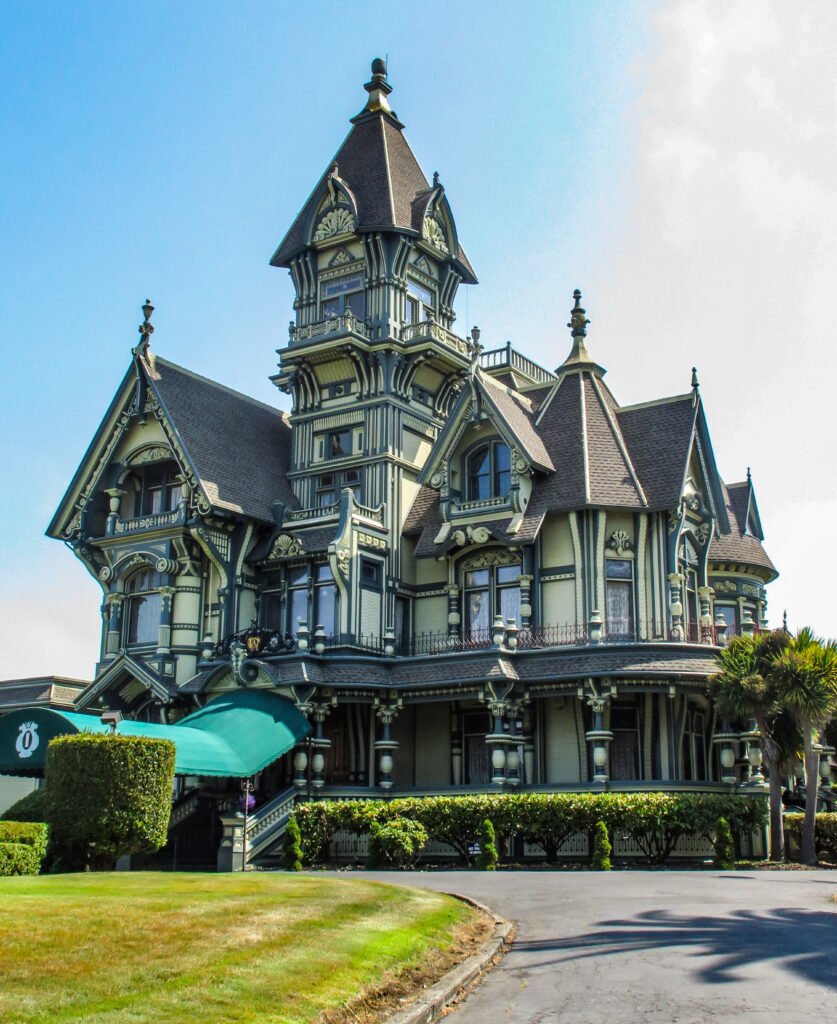
Hand Planes: The Craftsman's Essential Tool
Despite the rise of machine production, hand planes remained integral to the craft of millwork. They allowed artisans to refine machine-cut pieces, ensuring a smooth and polished finish. These tools, dating back nearly two millennia, evolved in design but remained fundamental in woodworking. The Stanley Rule and Level Company became a leading producer of high-quality hand planes during the 19th century, providing craftsmen with a variety of tools to shape wood precisely.
The role of hand planes in the Victorian era was particularly significant in finishing work. Carpenters used them to smooth stair treads, refine crown moldings, and add final touches to cabinetry. Even with advancements in steam-powered tools, no machine could replace the finesse that a skilled woodworker could achieve with a well-sharpened plane.
Transition to Modern Millwork
The 20th century brought further changes to the millwork industry. I would argue that not all of them were good.
In this article here, I talk about some of the big changes that came after 1950 in terms of the production and design of millwork in the United States.
The movement away from sharp edges in millwork is also an interesting phenomenon that was less influenced by the aesthetic of the moldings and more by the economics of milling profiles with sharp, pronounced edges. This article by ThisIsCarpentry covers this subject well.
As Bill Shaw, a custom molding millwright for over twenty years and the inventor of the Copemaster, puts it:
"Sharp crisp edges and profiles are harder to cut for several reasons. First, it takes more time to sharpen the knives. In order to get a sharp edge you have to have a very square edge on your grinding wheel—it must be dressed to a point. And the wheel must be redressed as it breaks down, which happens with greater frequency when cutting sharp-edged moldings. Second, the section of the knife that forms the point or sharp edge heats up more quickly, so the knife must be sharpened more frequently, and the molding can’t be cut at the same rate of speed. We typically ran moldings with radius edges at 30 feet per minute, but sharp-edge profiles had to be run much slower, at 20 fpm or even less. The speed is also affected by tear out, which is a problem at sharp intersections, requiring an even slower rate of feed."
We can observe that the degradation of mouldings was the result of economic decisions rather than just design aesthetic.
The development of new materials, such as medium-density fiberboard (MDF) and engineered wood products, offered alternatives to solid timber. The growing demand for housing, allocation of resources towards the war, and the rise of modernism as an architectural trend shaped the millwork trends in the decades after 1950. Ornate and intricate baseboards and crown moulding were often simplified or traded in completely for something like the clamshell baseboards stocked across big box stores nationwide.
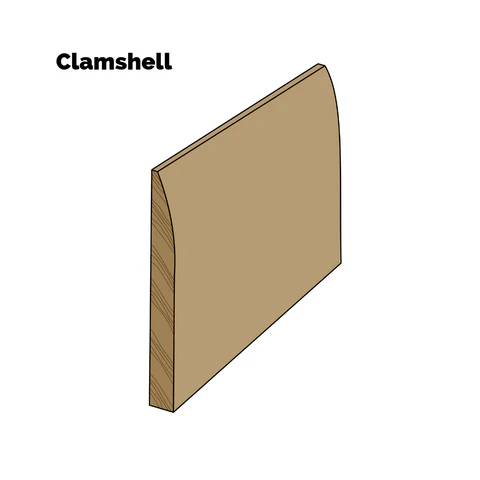
With the rise of the modern movement in architecture, millwork shifted away from excessive ornamentation. The clean lines of Art Deco and later Mid-Century Modern design resulted in simpler, more streamlined millwork products.
The International Style was the predominant influence in architecture at this time. It emerged in Western Europe during the 1920s, remaining influential until the 1970s. They took the principles of functionality and efficiency seriously and some might even say too far. The style emphasized minimalist design and modern construction techniques. For architects and designers following the International Style ethic, the goal of mouldings was to hide the joint where two surfaces met.
Companies like Georgia-Pacific and Weyerhaeuser adapted to the changing industry by focusing on large-scale lumber and engineered wood production rather than custom millwork.
Contemporary Millwork: Blending Tradition with Innovation
Today, millwork continues to evolve. On one hand, we have the modernist influence, which I think still has a stronghold on most academic architects and designers. On the other hand, I am beginning to see more carpenters, woodworkers, and designers ask the question.
Did we take modernism too far?
While the mass market for millwork is still dominated by speed of production and cost as the main factors. There is a Renaissance for tradition, companies like as Kuikenbrothers that are dedicated to producing millwork that is classical in design (designed pre-1950).
In the last several decades, there has been a resurgence in the demand for Historical Preservation and restoration and quality classical millwork is an integral part of that.
Other notable companies like Koetter Woodworking and White River Hardwoods specialize in high-end millwork, producing detailed moldings and custom woodwork that pay homage to historical craftsmanship. Restoration projects on historic Victorian homes also highlight the continued demand for period-accurate millwork, with specialists replicating original designs using both hand tools and modern machinery.
Final Thoughts
It's interesting to look through history and see the rise and fall of trends. Sometimes the forces that affect things such as the architecture and the homes we live in are distantly removed from us and it's only in retrospect that we begin to see the interplay of factors that affect an industry.
The history of millwork in the United States is a rich narrative of innovation, adaptation, and artistry. From its handcrafted origins to the integration of modern technologies, millwork has continually adapted to meet the aesthetic and functional demands of architecture and design. The Victorian era, in particular, stands as a defining period in millwork history, showcasing some of the most intricate woodwork ever produced. As we look to the future, the fusion of traditional techniques with contemporary innovations promises to keep the legacy of millwork alive, reflecting the enduring beauty and versatility of wood in our built environment.